知識丨天心天思制造執行系統(MES)
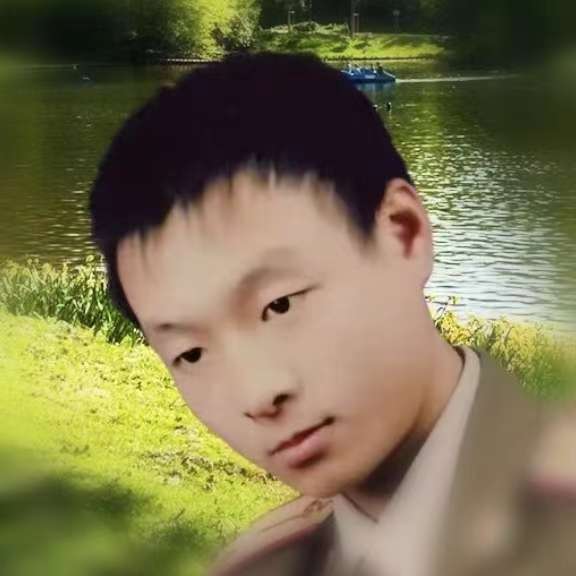
系統名稱:生產制造執行系統(簡稱MES)
隨著企業的發展,、管理問題也越來越突出。為此,公司在2007年實施了SAP的ERP系統,對財務、采購銷售、計劃和庫存等業務方面進行了管理,但在制造過程的管理中,還沒有一套系統來支撐。隨著汽車行業的TS16949認證管理要求,同時也出于企業自己管理的需求,需要一套制造執行系統來對制造環節中的物料、生產、質量、設備、關鍵部品批次跟蹤等方面進行管理和追蹤。
MES系統從SAP ERP系統得到工作工單,并將工作任令進行細化、調度、排產,對制造過程進行指引、控制,采集制造過程中的原料批次信息、生產信息和質量信息,并將采集到生產信息及時反饋到ERP中,從而使ERP及時掌握生產現場的信息。
在采集的信息的基礎上實現產品、部品之間的雙向追蹤和統計報表功能。在制造業信息平臺中,MES制造執行系統在計劃管理層與底層車間生產控制之間建立了聯系,填補了兩者之間的空隙。
MES系統主要有以下目標:
l 資源管理:通過對設備、物料、人員的綜合管理,平衡各方面的關系,達到縮短生產準備時間和生產周期,提高產品質量,全面提升設備利用率,大幅度提高生產排程和調度效率,更有效的利用車間資源,快速提升車間管理能力和管理效率,進一步降低生產成本,有效控制產品的質量問題,大幅度提高在制品追溯速度和準確性,工時管理更加科學合理,減少成品/半成品庫存積壓,縮短交貨時間,及時響應市場變化的目標;
l 生產調度:建立科學、實用的生產排程系統,幫助生產調度人員快速合理地進行生產調度,并可在情況發生變化時可以方便地隨時調整作業計劃,在保證及時交付的情況下,最大限度地節約生產能源,提高設備生產率和工作效率,減少產品總加工時間;
l 物料及批次管理:通過在線庫存和物料條碼管理,實現對生產物料的收、發、存、耗用管理,達到物料庫存、消耗和使用狀況管理,并通過對產品的制造過程和質量信息進行實時采集,實現產品的制造過程追蹤和產品與原料批次之間的雙向追蹤;
l 生產過程管理:控制指引制造過程,對產品各工序的生產、檢驗、維修以及交付過程進行控制和指引,在提高操作效率的同時杜絕作業操作錯誤的出現。實時監控生產,實現對生產過程的精細化管理和控制;
l 生產質量管理:建立完整的質量管理體系,對原料、生產、檢驗、交付各環節進行質量保障和質量跟蹤,提高產品質量。對缺陷及維修過程進行跟蹤和管理,實現有針對性的生產質量改進過程,滿足TS16949認證中質量管理要求;
l 生產設備管理:通過自動采集和人工輔助結合的方式,對生產設備進行管理,保障生產過程持續正常地進行;
l 文檔管理:控制、管理并傳遞與生產單元有關的信息文檔,包括工程圖紙、標準工藝規程、數控加工程序等。規范、唯一了工作中使用的文檔來源。增加文檔的查閱、修訂時的安全性、及時性和方便性。
l 現場監控:通過物料庫存監控、設備狀態監控、生產進度監控、質量狀態監控,提高現場管理的靈敏度;
l 自動化采集:通過與生產設備連接的自動化采集過程,實現了數據的集中管理和實時采集,減少了人工錄入的時間和差錯率,提高了數據的準確性和采集效率;
l 與其他系統的集成:與SAP之間實現自動數據交換,使訂單的各個執行環節在SAP中始終可視,提高SAP動態反映的能力,使生產供應各個環節更加協調。提供與外部其他系統的接口,實現與其他供應商/客戶的數據輸出;
l 數據分析和挖掘:通過生產過程大量采集的現場作業數據,提供滿足管理和業務的各類統計查詢報表,并為將來的數據挖掘提供詳實的數據;
MES系統功能:(7大功能)
1、1庫房管理
1.1.1 業務流程描述
1.1.1.1 原料條碼打印
對于有批次跟蹤要求的原料,在原料收到并經QC檢驗合格后,將物料折分到最小包裝,打印跟蹤條碼并粘貼在最小包裝上,建立原料與廠家條碼、廠家批次、是否環保原料、收貨日期等信息的關聯關系。
1.1.1.2 原料入庫
掃描已粘貼好跟蹤條碼的原料,錄入數量,建立對應的入庫單,記錄物料入庫人、入庫時間,原料完成入庫。
1.1.1.3 生產領料
按生產計劃通知單,開出領料單,倉管員提前套料(包括半成品)備好,放在的配倉區。實際發料時,將SAP中生產工單的發料清單導入到系統中,倉管員根據工單進行發料。發料時,掃描原料跟蹤條碼,建立工單與原料、半成品的對應關系。發料過程中系統對原料的條碼和數量進行校對,防止錯料、漏料、多領、少領等情況的發生。
同時系統提供了可供選擇的PDA指引式揀料模塊,該模塊通過工單的發料清單和系統中庫房原料存放的信息,通過PDA指引倉管員從倉庫中進行揀料備料。
1.1.1.4 生產退料
在工單加工完成后,按工單將剩余的原料進行退倉處理。工單退倉完成后,可以在系統中對該工單的原料消耗進行差異分析,分析是否有物料超損或丟失的情況。
1.2.1 概述
SAP中制定了月計劃,但SAP的計劃屬于高層次的計劃,無法對具體的生產工單在各個工序間的生產進行調度。MES系統的生產調度管理模塊,可以使用自動排產和手動排產對生產工單進行調度,安排每個工單在各個工序的具體生產線體、計劃開始時間和計劃結束時間,并根據庫房管理模塊提供的庫房原料庫存信息,進行物料齊套等可用性檢查。排產完畢后,通過排產結果發布,各授權崗位、角色可以在系統中馬上查詢到排產信息,并根據排產內容安排管轄崗位工作。
1.2.2 業務流程描述
1.2.2.1 訂單下載
MES從SAP系統中下載最近一周的生產訂單,在MES中生成生產工單。在下載的過程中,系統根據工單加工產品對應的標準工藝路徑,生成當前工單生產加工的各個工序信息及各個工序的參數信息。
系統提供人工下載和自動下載兩種方式。
人工下載方式根據人工輸入的工單號將SAP系統中的工單信息下載寫入到MES系統的標準工單信息中,并將物料已經齊套的工單狀態置為待產。當源工單信息的狀態不符合下載要求(工程狀態為確認、物料狀態為齊套或部分齊套)時系統提示操作者。
自動下載方式:定時(時間長度由系統設定)掃描SAP系統中的工單信息,搜尋未下載過的工單,滿足條件時系統自動將工單下載到MES系統中并將物料已經齊套的工單狀態置為待產。
1.2.2.2 訂單錄入
系統允許手工錄入非SAP中的訂單,錄入的訂單與從SAP下載的訂單在后續的加工過程中的業務流程和管理是一樣的。
1.2.2.3 工單維護
從SAP下載的訂單生成MES的工單后,僅僅只是根據產品標準的工藝路徑生成了當前訂單的工單加工信息,并沒有考慮一些特殊的情況。通過工單維護功能,可以對工單進行適當的調整。
工單的調整主要包括三個方面。一是工單身的信息,二是工單的加工工藝路徑,三是各個加工工藝路徑中,一些具體的生產過程控制、質量檢驗方法、生產質量預警等參數的設置和調整。
工單信息維護主要包括工單號、加工的產品、計劃生產數量、計劃開工日期、計劃完工日期及其他一些工單屬性的維護。
工序信息維護主要包括產品的加工工序(可以增加、插入、刪除產品的加工工序),每個工序可具體設置生產過程需要的控制和質量控制(如是否首檢、首檢標準、質量控制參數等)。對于未完工的工單,可以修改(增加或減少)計劃生產數量,進行追加生產或提前完成生產。對未開工的工序工單,可以刪除其工序或更改設置。
1.2.2.4 工單調度
生產調度排程使調度人員能夠在計算機系統的幫助下最優化地安排工單在各工序的加工,保障及時交付,同時保障生產線利用率最高,將工單安排到各個工序、各個線體上進行連續有效地生產。
系統提供了自動排產和人工排產兩種圖形操作模塊,自動排產采用業界先進的“遺傳算法”,根據待排產工單的工藝路徑、設備產能、運行狀態、人員配備等因素,自動尋優,找出次優解的排產結果。
手工排產使用交互性圖形化界面,易操作、直觀。工單某工序的加工時間根據產品工序的機臺效率、工單的批量大小、轉機種時間設置等條件自動算出,簡化了調度人員的低級勞動,提高了排產效率。
手工排產可以對自動排產的結果進行調整。排產的結果以表格和甘特圖兩種方式進行展示。
1.2.2.5 齊套檢查
根據工單調度確定的各個工單的加工順序,同時根據庫房管理系統中,當前各原料的庫存情況,根據工單的物料清單,逐一預檢查各個工單原料的齊套情況,并在排產的結果圖形中以顏色區分表示,使計劃能夠清楚整個生產的產能和物料的齊套情況,合理安排相關的生產活動。
1.2.2.6 排產結果發布
排產完畢后,通過排產結果發布,各授權崗位、角色可以在系統中馬上查詢到排產信息,并根據排產內容安排管轄崗位工作。
1.3.1 概述
工單經過計劃員排產發布后,已經確定每個工單在何時,在哪個工序的哪個線體上進行加工。MES指導物料員、庫房管理員及時進行揀料、備料和上料,同時也指導線長協調生產人員,對設備進行調試,指導條碼打印人員打印工單需要的產品條碼準備進行生產。并通過工單及文檔管理系統中相應的作業指導書,指導生產的順利進行。
在生產過程中,以條碼、RFID等信息載體,MES實時采集生產制造過程中的加工和質量信息,在采集的同時,將采集到的信息與工單、工藝路徑及參數、物料、質量等信息進行相互驗證,起到物料防錯、工序防錯防漏、工藝防錯的作用,同時也將采集到的生產及質量信息實時反饋到系統的各看板、SPC和統計報表中,使管理者在第一時間掌握車間的物料、生產進度、質量情況,為管理者的決策提供數據支持。
1.3.2 業務流程描述
1.3.2.1 工單單板、部品條碼打印
根據待加工的工單及批量信息,選擇適當的條碼生成規則,為每一塊主板、外殼、外裝盒、配件等生成生產加工過程中的唯一條碼信息并打印,并記錄這些條碼與工單的關系。在后續的作業過程中,需要在對每一塊單板或部品條碼掃描時,校驗工單與條碼的對應關系,防止生產加工過程中的錯誤。
1.3.2.2 SMT備料上料
工單在SMT工序生產所需的原料經庫房管理系統揀料并領料出來后,根據生產工單的備料指令,為SMT設備準備各物料,并進行上料操作。上料時,系統自動進行指引、校驗,防止上錯物料。
訂單(工單)上料必須檢驗原料的環保信息。如果訂單(工單)為環保,則不允許上非環保的物料。同時系統給出明顯的“警告”信息,以提醒操作員。
上料時,如果訂單(工單)料沒有上齊,則系統出明顯的“警告”信息,以提醒操作員。如果在此環節遺漏沒有控制住,則在該訂單(工單)加工的第一塊板進行檢驗時,系統再重新給出“警告”提示信息。
為實現SMT備料上料的業務,需要對SMT及附屬設備,如飛達、TABLE、TRAY盤進行條碼管理和運行維護管理(詳見設備條碼管理部分)。
SMT上料分為移動TABLE和固定TABLE兩類。
SMT工序的備料和上料過程,為進行物料批次跟蹤提供了最原始的信息。
1.3.2.3 其他工序上料
SMT工序由于設備的特殊性,需要經過多個步驟的操作。而在其他工序,例如插件、裝配、包裝這些工序環節,其上料過程相對簡單。操作員掃描物料根據系統提示確定是否為當前需要加工的物料,然后掃描工位,系統驗正合法性,物料與工位是否匹配。
通過以上幾個制造過程中對物料的管理模塊,保障了生產過程中物料使用的安全性,防止了錯料等情況的發生,特別是在環保/非環保工單/物料的加工過程中起到了非常關鍵的作用。
1.3.2.4 制造過程采集與控制
系統在各個工序的每條生產線上設有生產及檢驗采集點,分別采集質量檢測信息、維修記錄信息及各工序生產完工信息。
根據工單的加工工序及在各個工序上設置的參數,要求工單在加工過程中嚴格按照規程進行加工。在加工的過程中,系統指引各工序的下工序是什么并進行工序防呆:校核工序路線是否正確、上工序是否加工完成、上工序加工質量是否合格。對于不合規則的產品移動,系統及時提示用戶,并指引到正確的加工工序。
通過在各個工序的采集收集到的信息,得到了與制造相關統計報表的基礎數據。系統提供了多種數據采集方式:人工錄入、掃描條形碼、批量文件導入、與工控設備接口獲取、與其他生產/檢驗系統接口獲取等多種數據采集方式。
制造過程信息的采集主要分三類。一類是普通的加工工序,即產品經過該工序時,采集一個條碼信息,記錄了該工單、該條碼的產品在當前工序當前線體上的加工時間、操作員和相關的質量信息。第二類是裝配類加工工序,該工序除了要記錄第一類工序的所有信息外,還要記錄主板與外殼的關聯關系。第三類是包裝類加工工序,需要記錄產品與各種配件的關系,同時也要記錄多層的包裝盒與包裝箱之間的關聯關系。
1.3.2.5 在線維修
產品維修有兩種情況,在線維修和批量返修。按照工段可分為SMT修理/SMT外觀修理/補焊修理/ICT修理/FT修理/涂敷修理/板測修理等。在線維修由IPQC指引,批量維修則根據批量返修工單進行。產品維修功能主要對維修過程中的故障類型、故障原因、涉及器件、涉及人員以及維修狀態信息進行記錄。
當IPQC檢查產品有質量問題并進行了記錄,則該產品將不能再繼續到下工序加工,必須先要進行維修。維修員掃描產品條碼,系統自動列出該產品的所有待維修的缺陷信息:缺陷代碼、缺陷名稱、缺陷位置、元器件、缺陷數量、類型類別、缺陷發現所在工序、缺陷發現人等相關情況。維修人員可直接根據系統中IPQC記錄的缺陷情況對產品進行維修。維修完成后,將維修過程記錄到系統中。
修理更換器件需要自動比對工單與器件的環保屬性,防止非環保物料用于環保工單.
在維護的過程中,如果維修人員發現了檢驗人員沒有發現的缺陷信息,則由維修人員將新發現的缺陷信息錄入到系統中,同時對新的缺陷也可進行維修處理。維修完成后,產品重新返回原工序的檢驗人員處進行檢驗,此時,檢驗人員可以看到原檢驗人員錄入的缺陷,也可以看到維修人員錄入的缺陷,并根據缺陷和維修信息進行重檢。
1.3.2.6 產品報廢
對于無法維修等原因產品需要進行報廢處理,在系統中登記報廢產品的條碼、報廢原因,同時從系統中提取相關的生產和質量信息進行歸檔,以便進行分析和查閱。
1.3.2.7 產品隔離
對于一些原因不明的不良品,為防止流入下工序,可以進行產品隔離,以便進一步分析發生問題的原因。已隔離的產品,在任何工序上操作時,系統都會給出明確的提示,防止誤操作。
1.3.2.8 工單管控
由于生產環境中,各種可變的因素可能導致生產的暫停,因此,需要對工單進行各項控制。
工單控制主要有以下工作:
1)工單掛起和恢復生產
2)工單刪除
3)工單更改ECN
在生產過程中出現意外情況時將工單置為掛起狀態暫停執行工單的掛起有多種情況
1)首檢不合格經相關人員確認后將工單掛起
2)生產線上設備發生異常生產過程不能繼續
3)其他行政性因素
工單掛起后當條件發生變化需要繼續生產時將工單的狀態重新置為生產。
工單控制分為三個層次,分別為:
1)部門級工單控制:對整個工單進行控制;
2)工序級工單控制:對產品加工過程中的某個工序的工單進行控制,對當前工單的其他工序不產生影響;
3) 班次級工單控制:對產品加工過程中的某個工序的某個線體的某個班次的工單進行控制,不影響當前工單在當前工序其他線體的班次工單的生產;
1.3.2.9 作業指導書查閱
在制造的各個環節,可隨時在系統中調閱由MES文檔管理子系統提供的當前工單、當前工序的作業指導書和相關的產品資料,保證了制造的正確性和資料版本的正確性。
1.3.2.10制造過程相關看板
系統提供了在制造的各個環節,隨時監控制造過程中的生產進度情況、生產質量情況、設備運行情況、在線庫物料消耗情況等相關的各種看板,隨時了解現場的各種狀況。
1.4.1 概述
在MES中定義質量活動的流程和準則。
在制造過程中測量和采集質量信息。
按準則控制質量和業務流程。
通過SPC、SQC分析造成質量問題的根源,發現引發缺陷的趨勢。
找到防止問題在未來發生的方法,并對流程加以改進。
1.4.2 業務流程描述
1.4.2.1 定義產品質量控制工序
根據待加工的產品的加工工藝路徑,結合產品的質量特性,在加工的過程中,設置各種質量檢驗工序,以保證在生產的過程中對產品質量的監控。例如,某些產品在SMT生產后,進入AOI檢驗前,設備先進行人工目檢,以盡早發現SMT加工工序的質量問題,避免批量質量問題的發生。而某些產品由于加工工藝的原因,可能不需要進行ICT檢驗。
1.4.2.2 定義產品質量控制工序參數
在定義各產品的質量控制工序的同時,設備該質量控制工序的控制方式和參數。例如,對某些工序是否要進行首檢,各質量控制工序是隨機抽檢、批量抽檢還是全檢,檢驗的標準是什么。質量控制工序參數設置好以后,工單在加工時,就必須按設置的檢驗方式和參數進行檢驗,使得規則的質量檢驗能夠真正的落實執行下去。
1.4.2.3 首檢
當一個工單、一個作業班次開始加工時,為了檢驗設備的情況、用料的情況、產品的設計情況等,需要在各個工序首先加工3~5個產品,并對這幾塊產品進行質量檢查,以確保后續的生產能夠順利地進行。
當在工序質量控制參數設置中設置了要進行首檢時,系統自動根據檢驗規則進入首檢狀態,要求操作員完成首檢工作才允許進行批量生產。
不同的產品、不同的工序可以定義不同的首檢規則。
1.4.2.4 全檢
本功能供工序檢驗人員使用,完成質檢信息錄入、首檢結論處理、產生DPMO圖源數據、預警圖源數據等。
全檢過程必須對工序中一個產品進行檢驗,并根據檢驗結果錄入檢驗結論。
1.4.2.5 隨機抽檢
不定時地對各工序的產品進行檢驗,并根據檢驗結果錄入檢驗結論,并將檢查結果輸出過程警報信息。巡檢不合格品產品不能流到下工位,但巡檢不對被檢的批量產品進行判斷,產品正常流到下工位。
1.4.2.6 批量抽檢
批量抽檢是將一個生產工單的一個工序生產的產品,分成多個批次進行抽檢。
標準抽檢需要預先定義檢驗規則、檢驗標準和檢驗方案,并在生產過程中,根據檢驗方案對產品進行批量抽檢。在抽檢過程中,對抽檢的產品進行質量判斷。如果在幾個批次中都出現有質量問題,則需要增加后續抽檢批次的抽檢比例,達到加強質量控制的目的。如果連續多批抽檢質量合格,則可以減少后續抽檢批次的抽檢比例,達到減少生產成本,提高生產效率的目的。
在訂單(工單)的維護中,確定各工序批量抽檢的方案和抽檢的批次大小。系統根據批量抽檢的方案,在生產過程中指引檢驗人員進行批量抽檢。
1.4.2.7 巡檢
巡檢則是由人工確定巡檢的頻率和數量,不定時地對各工序的產品進行檢驗,并根據檢驗結果錄入檢驗結論,并將檢查結果輸出過程警報信息。巡檢不合格品產品不能流到下工位,但巡檢不對被檢的批量產品進行判斷,產品正常流到下工位。
還有一類巡檢不是針對產品,而是針對人、機、物、法、環的檢查,以保證生產的規范性。
1.4.2.8 檢驗設備結果采集
在生產加工的設備中,有部分自動檢驗設備,該設備的檢驗程序能夠自動對產品進行檢驗并生成檢驗結果。對這些檢驗設備的檢驗數據,系統自動進行采集,并與系統的檢驗進行接口處理,轉換成系統中產品的檢驗結果,以減少數據重復錄入的工作量,并且有效避免了人工數據采集時的出錯情況。
這部分信息主要包括:ICT/FT測試結果。
1.4.2.9 維修重檢
IPQC在檢查出產品缺陷信息后,送維修點進行維修(見制造過程管理-在線維修)。當產品維修完成后,必須返回到原發現缺陷的工序,經IPQC復檢合格后,才允許進入下工序,而不是維修后就直接進入下工序,以防止不良品流入下工序。
1.4.2.10批量隔離
產品在加工過程中,可能在前面的工序沒有發現質量問題,但到后面工序時才發現前面工序的質量問題,這時候一般已發生了批量的質量問題,需要將情況及時反饋到質量發生的工序,同時將已從質量發生工序流下來的產品全部進行隔離,防止再加工。再將這批有質量問題的產品的質量缺陷信息批量錄入,然后送修。
1.4.2.11質量管理相關看板
系統提供了在制造的各個環節,隨時監控制造過程中的質量情況的看板和報表,如工單質量看板、質量預警、DPMO、SPC,同時也為將來產品的質量追蹤提供了數據。




